Identifying Major Diameter
The major diameter can be measured with a micrometer, caliper or steel rule.
Major diameters are generally the first numbers found in thread designations. A 1/2-10 Acme thread, for example, has a major diameter of .500 in. Care must be taken to measure the major diameter on a section of the screw thread that is not worn.
A worn portion will measure smaller (or larger if burrs have been rolled up) than the original major diameter. Therefore, it is good practice to measure the major diameter and screw size over the least used section of the screw.
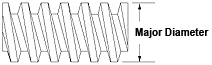
FIGURE 46
Identifying Minor Diameter
The minor diameter can be determined by direct measurement on an optical comparator or by measuring the depth of the thread with a depth micrometer and subtracting twice the measured depth of thread from the major diameter.
- When using a comparator to measure the minor diameter, remember that the reflected image is reversed (except on modern, image correcting comparators).
- This means that the bottom of the shaft is shown at the top of the screen. (See FIGURE #47)
- Often oil from the shaft runs down and collects on the bottom of the thread grooves increasing the shadow image.
- If the oil is not removed, a false (oversized minor diameter) reading will result.
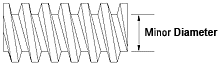
FIGURE 47