Wear Life Testing Methods
As mentioned before the best method of assessing the performance and life of Power Screws and nuts is actual field testing. This may present difficulties because of time constraints so accelerated lab testing is often conducted instead. When monitoring wear, all lab testing should monitor drive torque and nut temperature along with some method of regulating speed and load.
- Deadweight testers are popular and reliable.
- Hydraulic or pneumatic load testers can also be used but load cells are recommended to detect unexpected variations in the load pressure.
- The use of cooling fans is often necessary when artificially high duty cycles are used to shorten the testing duration.
Monitoring Wear
Most users measure the backlash in the screw and nut set both initially and ongoing during the life test (see Figure 42). Doing so will most likely produce a classic “S curve” graph similar to that shown schematically in Fig. 35.
New (Unworn) Screw
The section of the graph from point “A” to point “B” is the break-in section and is characterized by rapid initial run-in of the screw and nut surfaces.
- Both screw and nut surfaces are virgin at this point and some polishing of the surfaces occurs over a short period of time until the system reaches point “B” and begins steady-state or normal service wear.
- Normal service life continues until some point “D” after which the wear becomes quite rapid until the screw and nut seize or one member, usually the nut, fractures at point “E”.
- It is good practice to use a factor of safety and use point “C” as the practical service limit.
Many labs continue testing through point “D” to point “E” just to discover what can happen if service life is extended beyond the practical limit.
Old (Worn) Screw
Two points are noteworthy.
- The first is that the slope of the linear portion of the curve between points “B” and “D” is wear over time (the “K” factor in equation 2).
- The second is that point “C” is an arbitrary point of wear set by the judgment of the engineer or designer.
It may be an increase in the backlash, say a doubling of same, or it may be some portion, say 1/2 of the life between points “B” and “C”. The key is that at some point in time a decision must be made as to what constitutes a practical service life for each application considering the factor of safety, the failure mode and the consequences of failure.
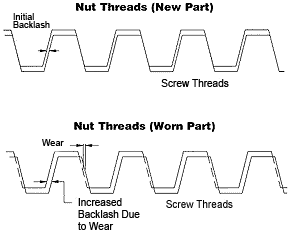
FIGURE 42